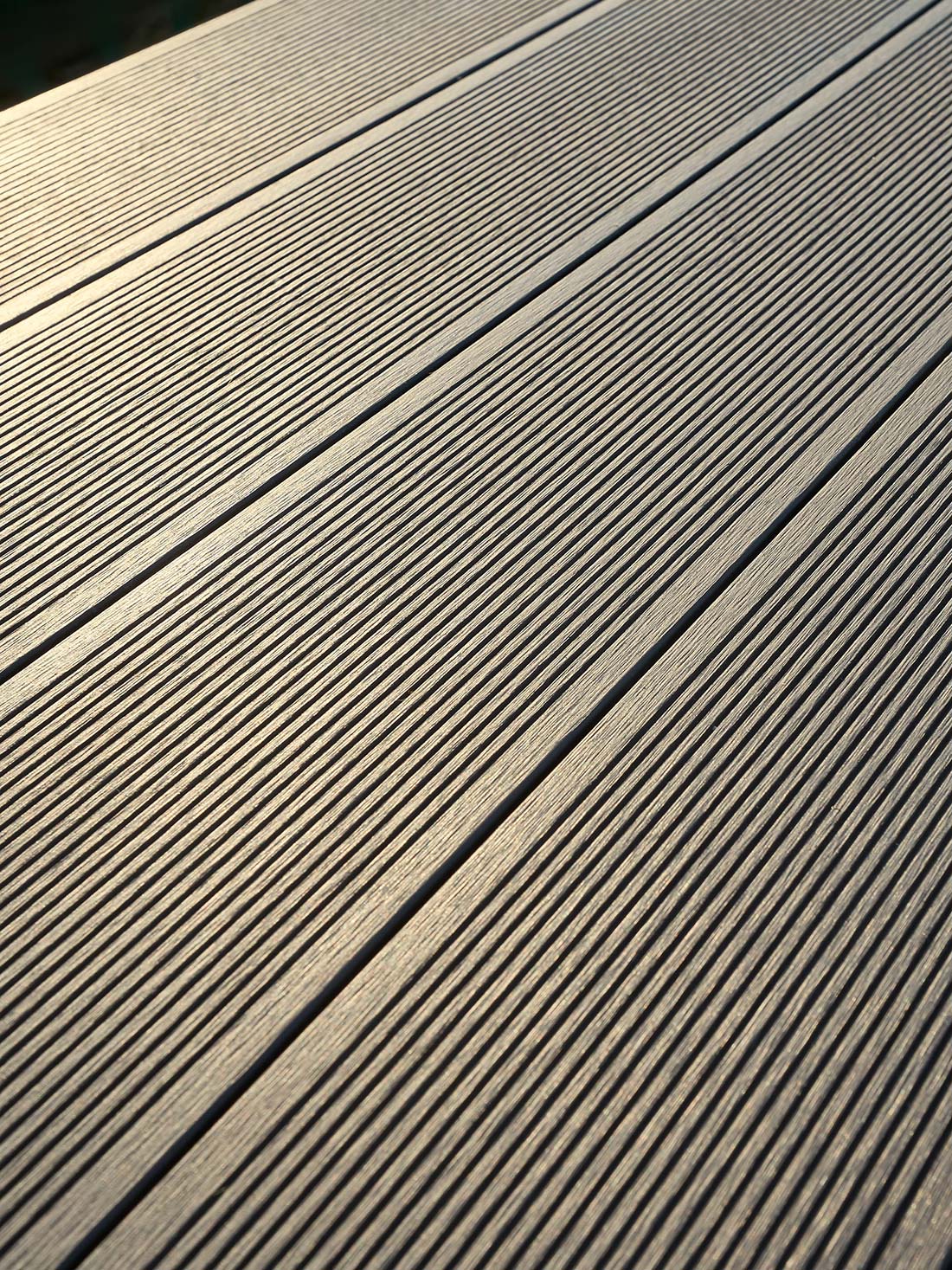
Structural plastic lumber is created to withstand the harshest weather conditions, commercial applications, and environments. With the varying product lines based on strength, recycled composite lumber is a fantastic alternative to concrete, wood, and metal. Even your most challenging projects can be tackled by structural plastic lumber.
Adding polymer or fiberglass strand when manufacturing plastic lumber can not only increase rigidity but create a durable product that is better suited for substructure components that require dimensional stability and a wider span. Due to the longevity and durability of structural recycled plastic lumber, the need to be replaced is nowhere near as often as more traditional building materials.
Ten Features of using Structural Plastic Lumber Products
- Cuts, drills, and secures just like wood
- Long life expectancy
- Various lengths
- Low maintenance
- No rotting
- No painting
- No splintering
- No staining
- Environmentally friendly
- Continuous piece construction
AVAILABLE PRODUCTS
- Wine Grape Stakes for wineries
- Construction Stakes
- Tree Stakes (agriculture stakes)
- Fense Stakes
- Fencing Lumber
- Beams
- Decking
Designed for Lasting Performance
Now that we’ve gone through the features and benefits, now we’ll go through the process of how recycled plastic lumber products are made. At Green Solutions, we have a pretty straight-forward process to create structural plastic. From gathering the materials and filtering out the unwanted items and paper labels, we will ensure that each structural lumber’s length is coloured textured consistently throughout.
Manufacturing Process
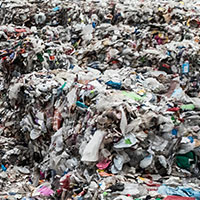
Gathering Raw Materials
The materials used are recycled HDPE plastic from post-consumer and post-industrial waste. These recycled plastic items include shampoo bottles, butter and yogurt tubs, industrial containers, milk jugs, juice bottles, motor oil bottles, and water tanks.
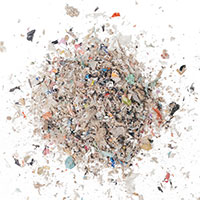
Preparing for Extrusion
Once we receive bales of recycled material, we break the materials down through our unique filtering process to remove paper labels and other items unwanted in the structural composite lumber mix. Filtering out the unwanted items makes it easier to put through the extrusion process due to the material being raw and without anything to disrupt the material’s integrity.
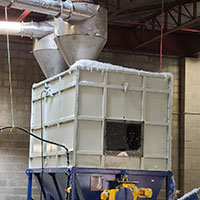
Extrusion Processes
Depending on the rigidity and strength of your project needs, at Green Solutions, our structural lumber products are put through either a Multiple Stage Extrusion or HardTool process. To have the colour and texture consistent throughout the lumber products’ full length, additional material such as colorant, strengtheners like polymer and fiberglass strand, and UV stabilizers are added during either process. This ensures the end-product will be entirely consistent.
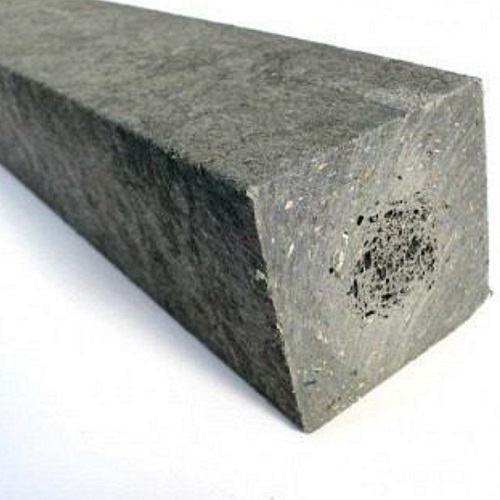
Finished Product
After going through either process, the final product is a long-lasting, durable recycled plastic lumber. The lumber can then be constructed to fit the specific needs of any design or project. At Green Solutions, we offer a vast selection of products to choose from, regardless of structural application. You can choose from a large selection of colours to match the aesthetic you’re searching for.